Whitehorse Fabworks recently completed several fixtures for a local building panel manufacturer. The developing industry of prefabricated building panels is proving to be a promising new frontier for building contractors. It is with a sense of great satisfaction that we reflect on the opportunity to partner in this industry.
Whenever someone can improve mass production on pretty much anything, they can usually drive down its cost. At the same time, they can often improve the product’s quality. In the 1890’s, Henry Ford discovered this miracle in his assembly line and made a product more affordable and more accessible to more people. However, he also set an ongoing standard of continued innovation for many other industries. The idea that those who are serious about manufacturing should always be looking to improve their processes is a kind of manufacturing science that we have come to expect. This same philosophy is what guides the prefabricated panel industry today in revolutionizing the construction process. Instead of doing all the construction on-site, the project is manufactured, as much as possible, in the controlled environment of the panel factory. The more things that can be carefully planned and figured out ahead of time, the fewer problems arise later. The more wasted movements and wasted raw materials can be eliminated, the more costs can be reduced. The more processes that can be automated, the more advantages there are for everyone.
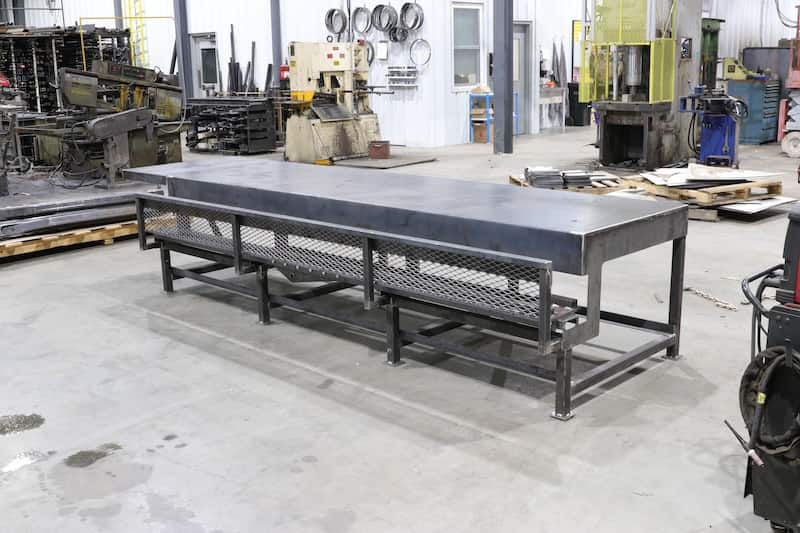
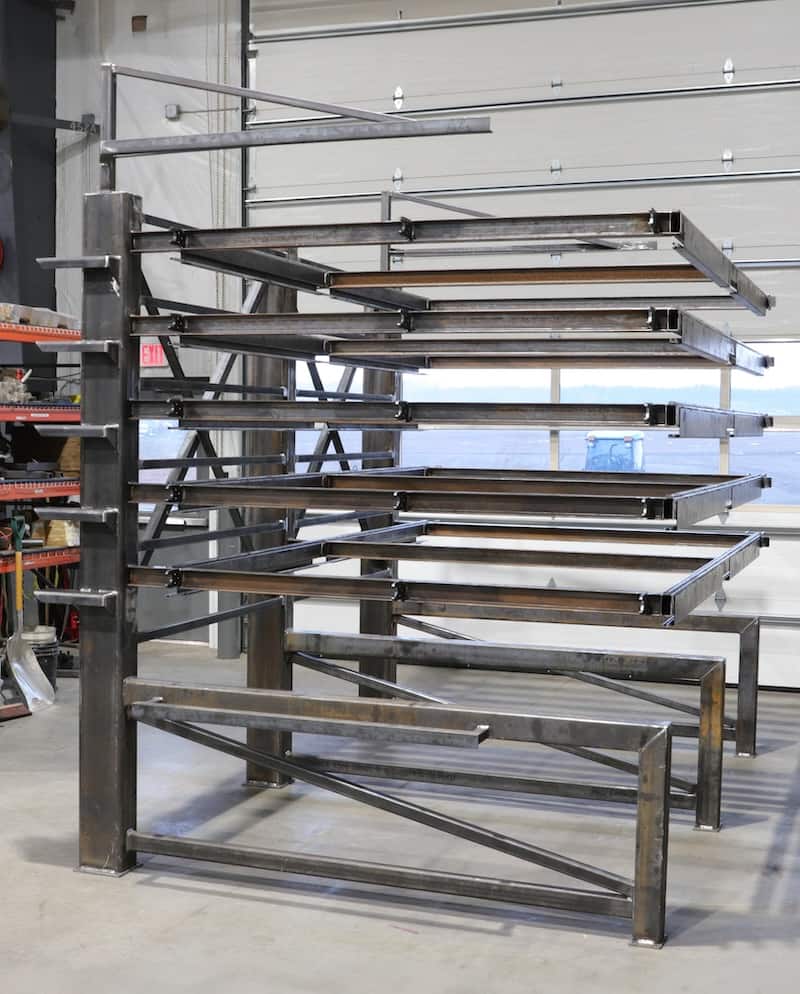
Modern technology has made a lot of the features of prefabricated construction a more viable process than it has ever been before. The first step in the process of prefabricated construction is what some prefabricators call a virtual build. In a level not typical of conventional construction, all the plan details are coordinated into the virtual build software where everything is taken into consideration. Rather than all the frustrating and costly discoveries of conflicts between foundation plans, architectural plans, site plans, and utility plans happening in the field, the panel prefabricator will coordinate virtually everything in his digital prototype. In many of these prefabricated panel factories, the finalized virtual build can then be pushed out to the CNC cutting machines. After receiving all the measurements and cut lists from the virtual build, the CNC cutter begins cutting out each of the pieces. Some of the more advanced systems even print on the pieces as they pass out of the machine and automatically mark them with the measurements they will need in the assembly line later. An automated system ensures efficiency and accuracy throughout the process fabrication process can also save a lot of materials, as the software’s algorithms calculate the best way to get the pieces out of the raw material with minimal waste. One fabricator noted, “The drop waste from an entire house usually only fills a couple of garbage cans.”

Not only do prefabricated panels offer advantages to the planners, but they also pay dividends on the job-site. By moving more of the construction process indoors, the impact of bad weather to the project schedule can be minimized. Door and window openings can be constructed with more accuracy creating consistent margins around the framing and windows or doors, which allows for a better insulation job. Shortening the amount of time spent on the framing stage of construction shortens the amount time raw materials are exposed to weathering. Finally, by not having stacks of raw materials sitting on-site, the risk of job-site theft can be minimized.
When considering the advancements that have been made, not only in the prefabricated panel industry, but in many other industries over the past few decades, it makes one wonder what will be next? Many commonplace innovations that we have today have only become a reality because someone was willing to do something that no one else had ever done. Someone was willing to take a risk. Someone was willing to be a pioneer.
Whitehorse Fabworks remains dedicated to partnering with these kinds of people.